The ceramic nozzle has the characteristics of sucking and spraying, and it can also be called a capillary tube because of its small holes.
Sucking nozzle is mainly used for the handling and positioning of components. During the “pick and place” process, the nozzle can effectively pick up and place electronic components.
Spraying nozzles are commonly used in jetting nozzles and dispensing nozzles to dispense adhesives or other materials on moving substrates at high speeds, ensuring accuracy and consistency for each component.
Jetting nozzles are used in a wide range of applications, such as cleaning equipment, spraying processes, cooling systems and chemical treatments. Their design and use can be divided into the following categories:
Round nozzle: usually used in situations where concentrated spraying is required.
Flat Nozzle: Suitable for applications requiring diffuse spray.
Adjustable nozzle: Provides flexibility to adjust spray angle and flow rate according to needs.
Dispensing nozzles are mainly used to accurately distribute liquid or paste substances to specific locations. These nozzles are widely used in electronics, medical, food packaging and other industries to improve production efficiency and product quality. Their design and use can be divided into the following categories:
Round nozzles: suitable for even distribution of liquids, often used in paint and glue applications.
Flat nozzle: Used when wide dispensing is required, such as sauce dispensing in food packaging.
Micro-volume nozzle: Designed for precise control of small doses of liquid, commonly used in glue applications for electronic components.
About ceramic materials
Alumina and zirconia are the two main materials used in the manufacture of ceramic nozzles, each with different mechanical strength and injection molding properties.
The flexural Strength of alumina is 350 MPa. (More)
Parts with complex shapes can be produced through ceramic injection molding (CIM) technology, and high precision can be maintained during the molding process.
The flexural Strength of zirconia is 1000 MPa. (More)
In terms of mechanical strength, it is more superior, and ceramic injection molding (CIM) is the best. Zirconia generally has higher flexural strength and toughness than alumina, which makes it more advantageous in situations where it can withstand impacts and high loads.

About specification and tolerance
Usually individual round holes can use “Wire grinding” to improve the accuracy of the hole, with a concentricity of 0.005mm.
**The alumina holes are 0.022~0.60mm, and the tolerance is +/-0.002mm.
**The zirconia holes are 0.080~0.60mm, and the tolerance is +/-0.003mm.
Our products
Glue dispensing nozzle / Jetting
How to present the right solutions to customers
The accuracy of ceramic nozzles can be further improved using X-ray technology. X-ray can provide detailed images of the internal structure, helping engineers check the internal flow channel structure of the nozzle to ensure the rationality and functionality of its design.
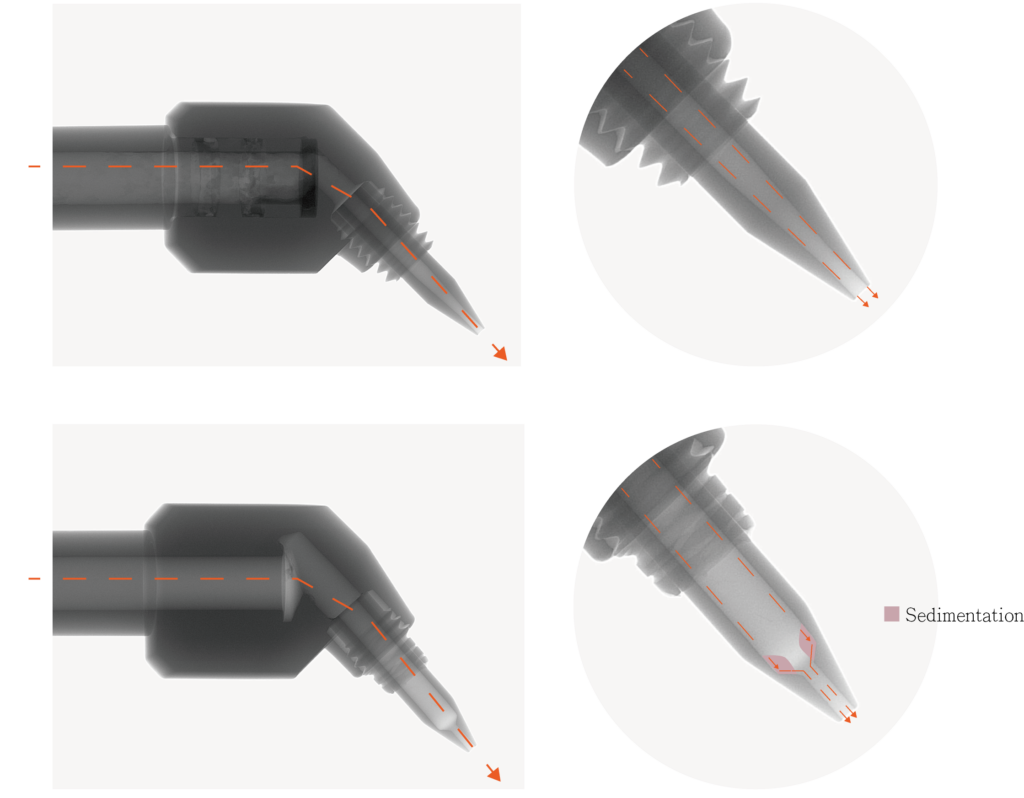
Why choose LONGYI?
PRECISION MEASUREMENT
LONGYI uses an X-Ray method to ensure the quality of shipment. Reverse engineering services also use this method to prevent damaging the workpiece. (More)