
The end effector of the ceramic vacuum type and mapping type are made of high-purity ceramics, which have excellent wear resistance and chemical stability. The vacuum type and MAPPING type are designed for special applications. widely used in semiconductor, optoelectronics, and solar energy manufacturing processes.
Ceramic end effector can be divided into contact type, vacuum type, vacuum + nozzle type and mapping type.
Contact-type end effector are usually supported by direct contact through the weight of the object.
Vacuum-type end effector use vacuum suction to grab and handle wafers. This design can effectively handle wafers of various shapes and sizes, especially thin or warped wafers, which are not possible with traditional vacuum chucks. can not achieve. These vacuum-type actuators are designed with high purity and low metal impurities in mind to avoid contamination of semiconductor materials.
Vacuum + nozzle type ceramic end effector combine the benefits of vacuum suction with the versatility of a nozzle system. This design is particularly effective for handling a variety of sensitive materials, including wafers, in semiconductor manufacturing.
Features and Advantages (More)
Antistatic ceramics also call Electrostatic Discharge (ESD) Protection:These end effectors utilize anti-static rubber nozzles to effectively prevent static electricity from damaging semiconductor materials. Electrostatic discharge can lead to material damage or performance degradation, making ESD protection critical.
Versatility:The nozzle design allows these end effector to adapt to different shapes and sizes of materials, easily handling both flat wafers and specially shaped components.
Stable Gripping Force:By combining vacuum suction with the flexibility of rubber nozzles, this design provides a stable gripping force, ensuring that no damage occurs to the materials during operation.
Mapping-type end effector are usually equipped with mapping sensors that can accurately locate the position of the wafer to ensure that errors do not occur during handling. This type of actuator is particularly important in automated production lines, as they increase production efficiency and reduce the risk of human error.
Vacuum-type ceramic end effector
Vacuum-type ceramic end effector are often used to grip and handle sensitive materials such as wafers. The high strength and lightweight properties of ceramic materials allow these devices to provide stable support during operation without causing damage to the wafer. In addition, ceramic silicon carbide helps prevent the impact of static electricity on semiconductor components, which is critical in semiconductor manufacturing.
Mapping-type ceramic effector
Mapping-type ceramic arm focuses on precise positioning and handling, especially in automated production lines. Such arms are usually equipped with high-precision sensors and control systems to enable efficient handling and positioning. The low thermal expansion coefficient and high thermal conductivity of ceramic materials allow these arms to maintain stable performance in high-temperature environments.
What are the advantages of using end effector and arms made of ceramic materials compared to metal materials?
1. Alumina, Al2O3 (Aluminum oxide) has extremely high hardness and rigidity, which allows them to maintain stable performance under high pressure and high temperature environments. Often used in wafer growth furnace tubes.
2. The corrosion resistance is better than that of metal materials. Ceramic arms are resistant to acid and alkali attack. During etching and thin film deposition processes.
3. Excellent insulation performance, which can effectively prevent metal ions from contaminating semiconductor components.
4. The lightweight characteristics make the robotic arm more flexible during operation and can improve production efficiency.
5. Features high precision and stability.
Ceramic end effector - contact type
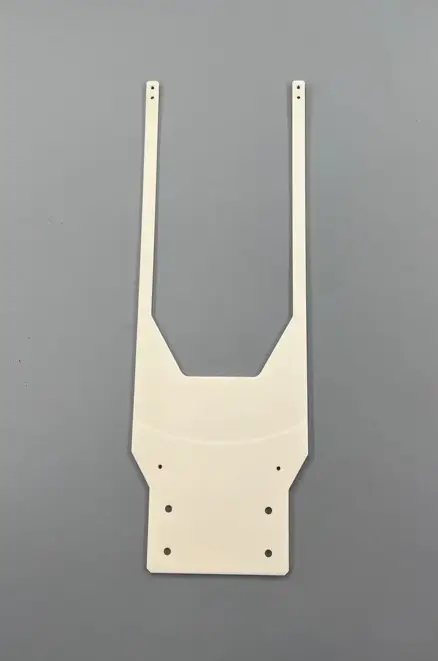
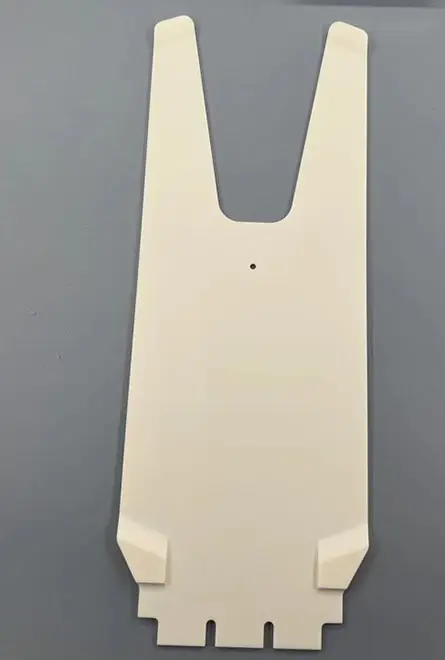
Ceramic end effector - vacuum type


Ceramic end effector-vacuum+Nozzle type


Ceramic end effector - mapping type

Materials of Ceramic End Effectors
Ceramic end effectors are made from various materials, each offering unique properties that make them suitable for specific applications in semiconductor manufacturing. Here are descriptions of three common materials:
Alumina (Al₂O₃)
Properties: Alumina is known for its excellent hardness, wear resistance, and chemical stability. It has a high melting point (around 2050°C) and good electrical insulation properties.
Applications: Due to its strength and durability, alumina is often used in environments where mechanical wear is a concern. It’s suitable for applications requiring high purity and resistance to chemical corrosion.
Advantages: Alumina is relatively inexpensive and widely available, making it a popular choice for many industrial applications.
Zirconia (ZrO₂)
Properties: Zirconia is characterized by its high toughness, thermal stability, and low thermal conductivity. It exhibits excellent resistance to thermal shock and can withstand high temperatures (up to 2400°C).
Applications: Zirconia is often used in applications where high mechanical strength and resistance to wear are critical. It is also utilized in dental ceramics and as a thermal barrier coating.
Advantages: Its ability to maintain strength at high temperatures and its resistance to crack propagation make zirconia ideal for demanding environments.
Silicon Carbide (SiC)
Properties: Silicon carbide is renowned for its exceptional hardness, high thermal conductivity, and resistance to oxidation. It can endure very high temperatures (up to 1600°C) and has excellent electrical properties.
Applications: SiC is commonly used in high-performance applications, including semiconductor manufacturing, due to its ability to handle extreme conditions. It is also used in abrasives and cutting tools.
Advantages: The combination of high strength, thermal stability, and resistance to chemical attack makes silicon carbide an excellent choice for applications involving sensitive materials.
Antistatic Properties of Materials
LONGYI offers ceramic materials that inherently possess antistatic properties. These materials are designed to minimize static charge accumulation without the need for additional surface treatments. Their built-in antistatic characteristics make them ideal for handling sensitive components in semiconductor manufacturing, ensuring protection against electrostatic discharge.
By utilizing these advanced materials, LONGYI ensures that your ceramic end effectors are ready for high-demand applications while maintaining excellent ESD protection.


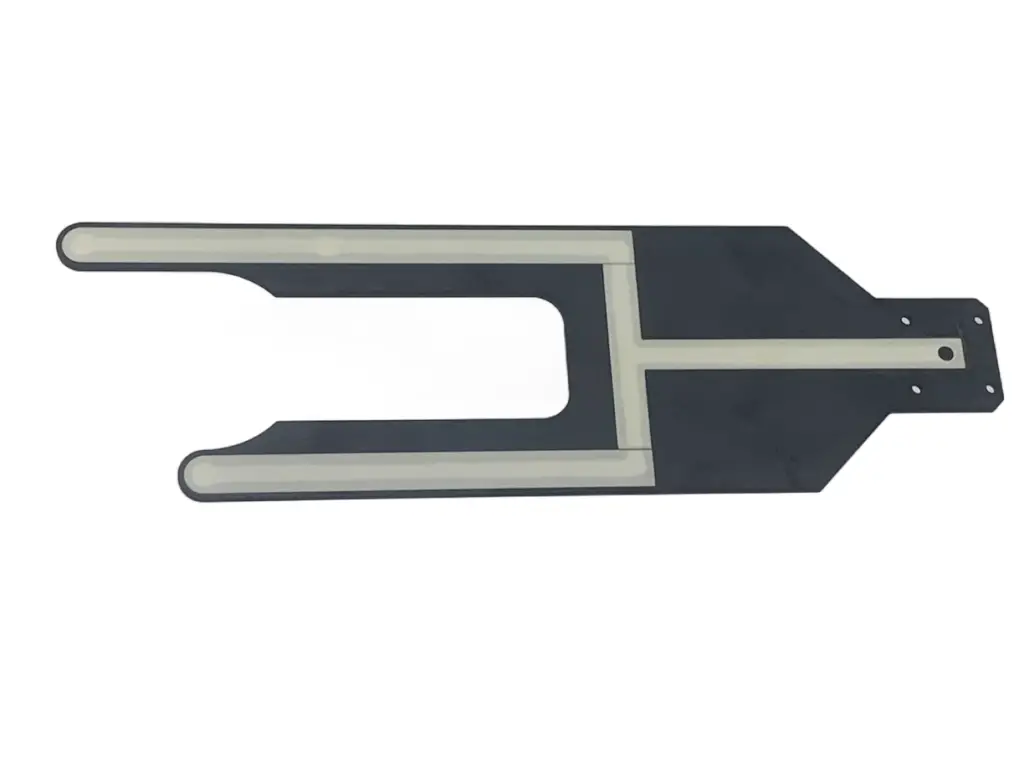
Surface Treatment and Electrostatic Discharge (ESD) Protection
Surface treatment technologies can effectively enhance the electrostatic discharge (ESD) performance of ceramic end effectors. By applying specific coatings or treatment methods, static charge accumulation can be minimized, protecting sensitive materials from damage caused by electrostatic discharge.

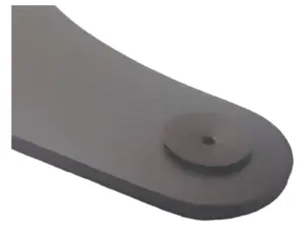